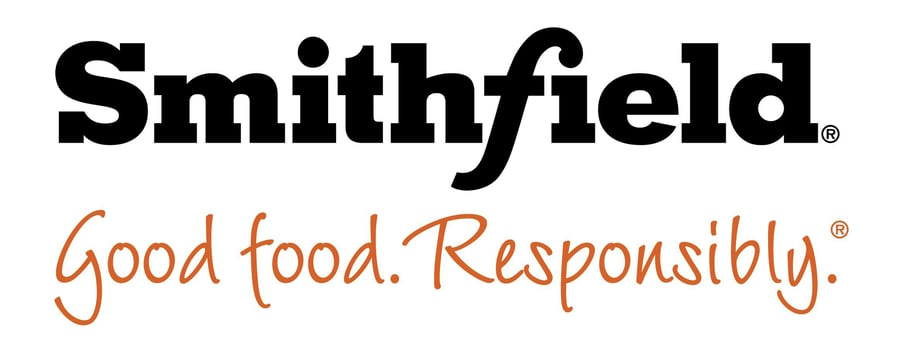
How Smithfield solved its problem with lost tools and cross-contamination risks by utilizing shadow boards
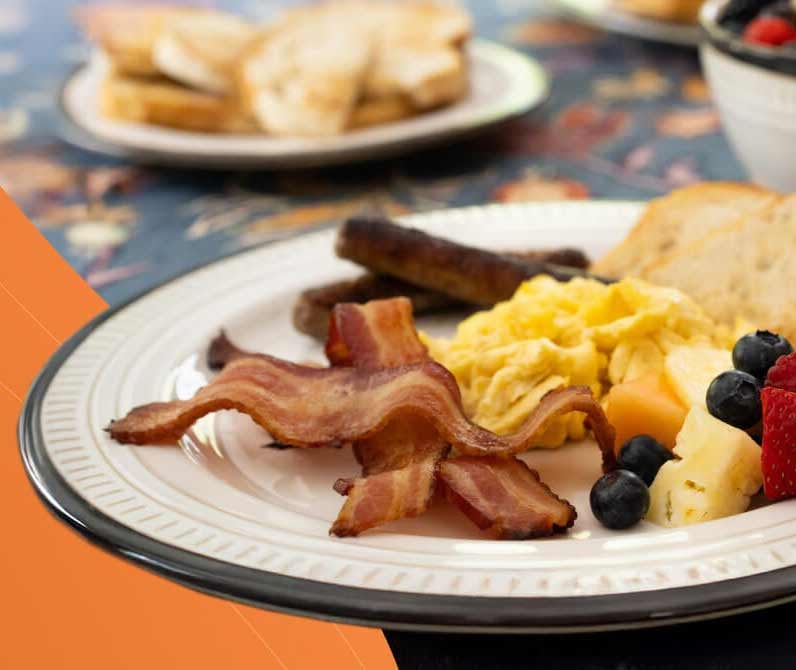
Industry
Food Manufacturing
Challenge
Smithfield faced significant operational challenges due to lost parts and cross-contamination during sanitation cleaning cycles. Despite implementing third-party sanitation services and stringent protocols, production and sanitation workers continued to misplace critical parts, leading to accidental damage and food safety risks. This issue led to significant waste, including lost equipment, production downtime, and discarded food.
Results
Smithfield overcame the obstacles of missing parts and cross-contamination by introducing shadow boards. This straightforward yet impactful solution minimized time wastage and notably enhanced safety. It is estimated that 88K/day in lost production time, downtime, and machine parts were recovered. The positive impact on employee morale was evident. Looking for parts saves about 15 to 30 minutes, resulting in approximately $11,000 in savings with the cost of line time.
Shadow boards
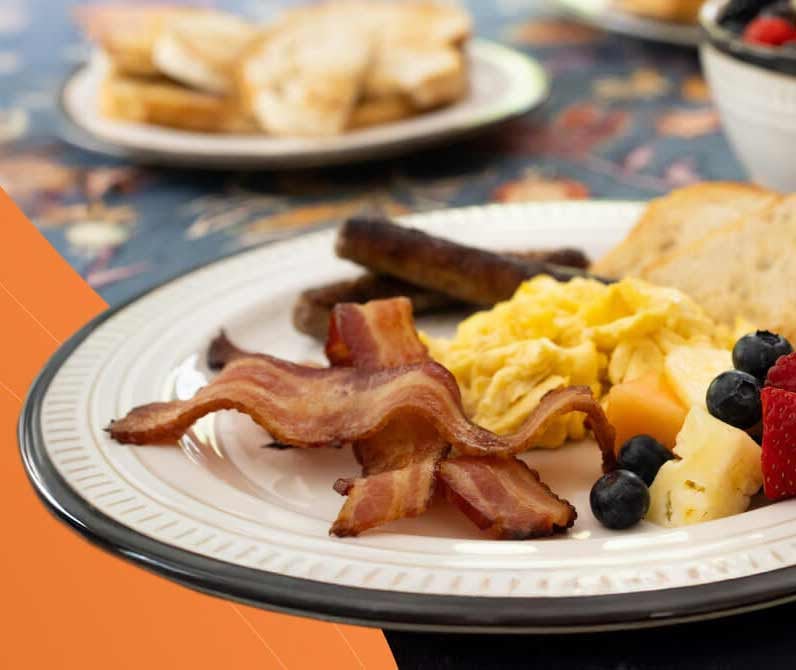
About your Customer
Since 1936, Smithfield Foods has been a staple on breakfast, lunch and dinner plates for millions of Americans and people around the world. Today, we're no longer just a food company — we've evolved into a clear leader in packaged meats, uniquely positioned to creatively meet the many flavor, occasion and packaging preferences of today's — and tomorrow's — consumers.The Challenge
Smithfiled was having problems with lost parts and cross-contamination during sanitation cleaning cycles. The plant was using a third-party sanitation partner (as many plants do), despite all efforts to tell production & sanitation workers to not loose parts, they were still going missing and even sometimes being accidentally ground up. This was causing significant waste (both of the parts & food waste) as well as greatly increasing food safety hazards.
The Solution
The plant partnered with Amerisan to create shadow boards for the parts that were removed during changeovers and sanitation cleaning cycles.
"The two employees that use the shadow boards love them. Saves about 15 to 30 minutes on looking for parts."
The Results
After implementing shadow boards, the plant was able to reduce time wasted by $11,000 per day. The plant also saw a significant improvement in safety. There were no more reports of lost parts or cross-contamination. In their own words, "So approximately $11,000 savings with the cost of line time, plus lost parts cost. All shifts love the boards"
Shadow boards in this application solved a persistent problem that the plant had struggled with for years and saved both labor and production time while reducing FM risk and product waste.