Shadow Boards: Cutting Tool Replacement Costs for Airline Catering
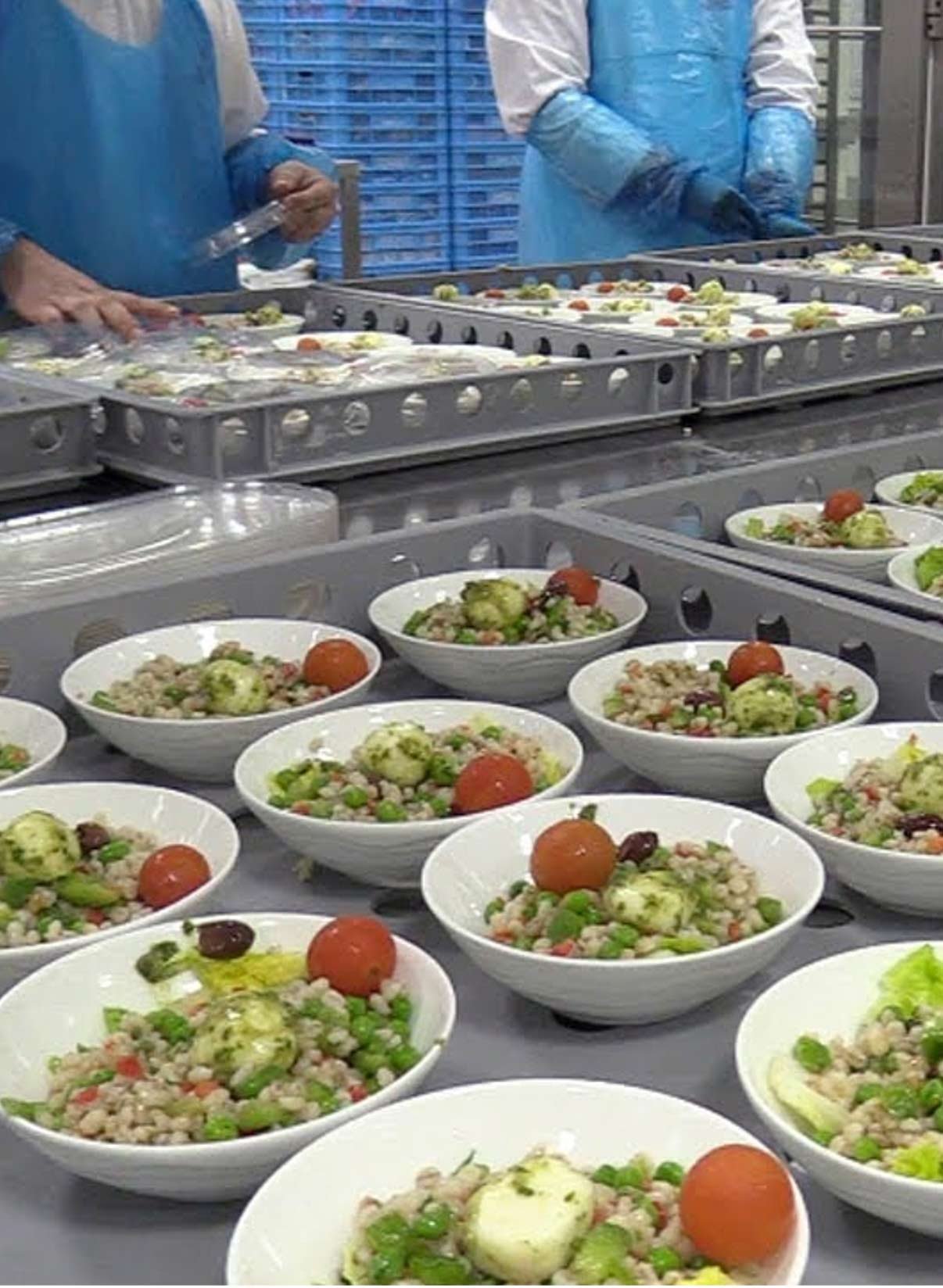
Industry
Food Service
Challenge
The catering services at Newark and JFK airports were facing problems with the organization and accountability of their tools, leading to frequent loss, misplacement, or damage and costing the company money.
Results
Following the implementation of shadow boards at the JFK location, our client achieved savings exceeding $12,000 in the first year and experienced zero tool reorders for 12 months. In contrast, the Newark location, without shadow boards, continued to order tools monthly. Consequently, JFK significantly reduced tool replacement frequency and improved employee efficiency in locating necessary equipment.
Shadow boards
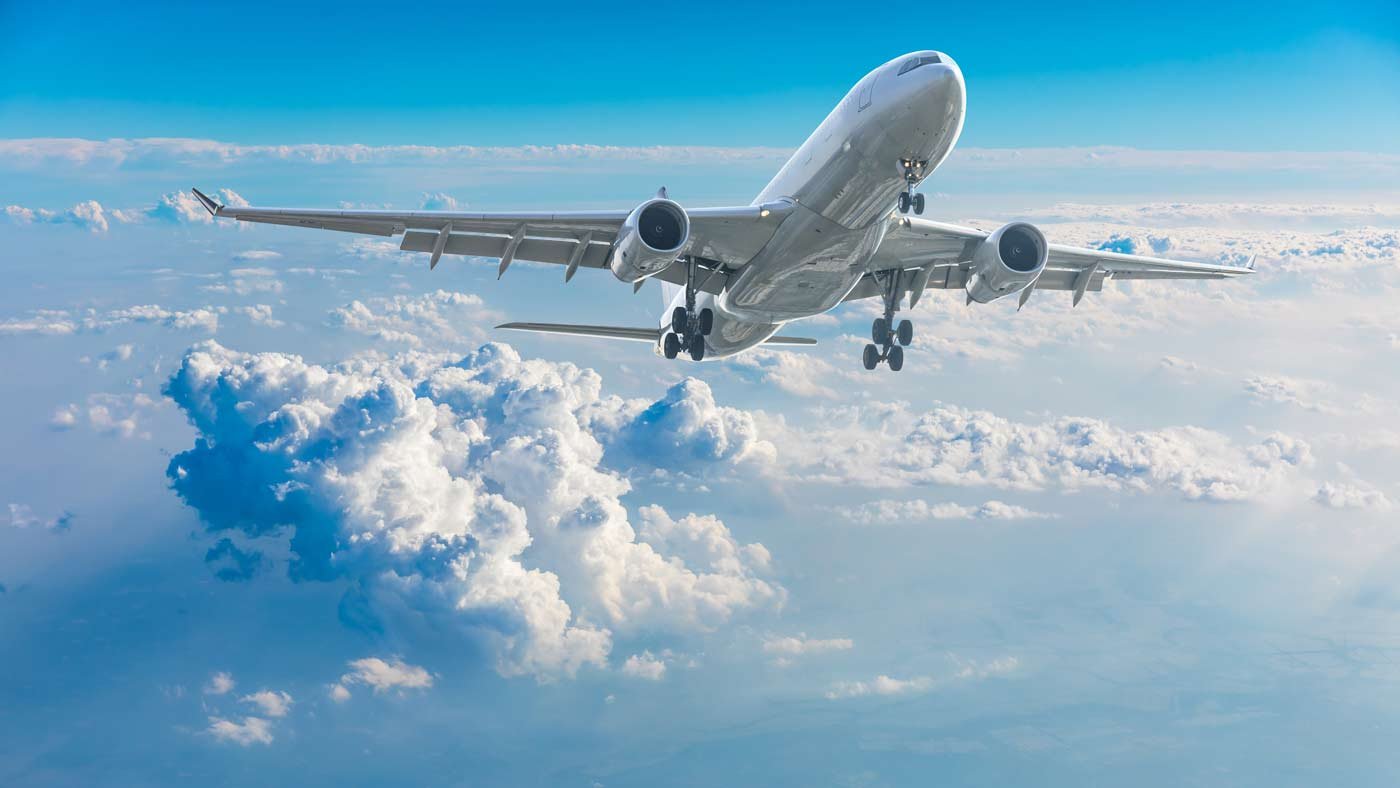
Breeze Airways* (name changed for privacy)
A national airline operating within the United States, the customer serves a diverse mix of business and leisure travelers. Facing increasing pressure to optimize its catering operations at major hub airports, the airline sought solutions to improve the efficiency and accountability of lost equipment.
The Challenge
Airline Kitchen faced significant financial losses at its Newark and JFK airport locations due to frequent loss, misplacement, and damage of color-coded tools. This lack of accountability disrupted operations and increased expenses.
The Solution
To address this challenge, Amerisan implemented a targeted approach. At the JFK location, color-coded shadow boards were introduced as a visual management system. Additionally, both the JFK and Newark locations were provided with the necessary tools. Shadow boards offer a clear visual outline for each tool, ensuring proper storage and immediate identification of missing items.
The Results
The implementation of shadow boards at the JFK location yielded remarkable results. Within the first year, the client realized savings exceeding $12,000 due to the elimination of unnecessary tool replacements. Notably, the JFK location did not require any tool reorders for a full 12 months. In stark contrast, the Newark location, which did not adopt shadow boards, continued to order tools every month, highlighting the direct correlation between the visual management system and tool accountability. Employees at JFK also benefited from the streamlined organization, enabling them to locate tools quickly and efficiently.
Key Takeaways
This case study demonstrates the effectiveness of shadow boards as a simple yet powerful solution for improving tool accountability and achieving substantial cost savings. By providing a visual framework for tool management, shadow boards minimize loss and damage to tool and equipment, leading to significant financial benefits for organizations of any size. The contrasting outcomes at the JFK and Newark locations highlight the impact of utizing visual management & 5S solutions.